Sprinkler System Design (BS5306: Part 2)
- Tan Yoke Lee
- Sep 6, 2018
- 4 min read

Sprinkler system design can be quite methodogical. In fact Engineers can learn to design without quite understanding the engineering facts behind the methods established in various BS standards and NFPA standards, thus the susceptibility of making subtle mistakes that could be catastrophic in the event of actual occurance of fire. This article discusses the various issues and challenges faced by engineers when designing sprinkler system in buildings.
The first issue that engineer would need to address is whether sprinkler is required in the building. This is easily addressed in our building by law code (UBBL, 1984) with latest revision incorporated by Jabatan Bomba dan Penyelamat Malaysia in schedule tenth. However, this does not address the issue that when sprinkler is not appropriate for the building designed and other alternative fire extinguishing system is required. Examples are areas with high ceiling areas, the sprinkler may not even activate when the designed fire size is small. We have done some calculation with CFI calculator and our findings are as follows:-
For 5MW fire which is normally the design fire size for shopping malls, the sprinkler would not activate at 16m height. For a 15m height ceiling, installing a quick response sprinkler could only activate the fire after 80second with ceiling jet temperature of merely 69.7 deg C. This is in comparison of the activation temperature of sprinkler which is 69 deg C. With slight deviation in site situation, the sprinkler may not even discharge ifthe ceiling jet temperature becomes less than 69 deg celsius where the sprinker is installed. Rarely would the design fire size be more than 5MW except for warehouses and factories handling combustible materials as raw materials or their products.
Next assuming that sprinkler has been prescribed for the premises, it is important to identify what hazard to assign to the building in terms of sprinkler features design. There is actually very little guide lines in BS5306 for this matter except the followings:-
a) Non industrial areas with low combustible contents and fire loads and rooms less than 126m2 and walls of not less than 30mins fire rating can be classified as light hazard. That being said, in Malaysia where sprinkler is prescribed in schedule tenth, the criteria of less than 126m2 per room is seldom fulfilled. As an engineer, I personally would never design light hazard as there is also a danger of future refurbishment where walls are knocked down to create areas more than 126m2, the entire system would have to be changed.
b) Non industrial and commercial areas that do not fulfill the light hazard criteria would normally be classified as ordinary hazard. Similarly for industrial and commercial areas where the fire load is expected to be medium and the building contents are of medium combustibility, ie unlikely to develop into an intense fire in very short time. Table 3 of BS5306 can be referred to for some examples of how to classify ordinary hazards, group I, II and III.
c) Industrial and commercial areas with high fire load or combustible contents are classified as high hazard.
When goods are stacked up high, there is a table guidance in BS5306 on how to further classify the storage premises into ordinary III hazard or high hazard in accordance to stack height and nature of goods.
Having said the above, there is no prescribed method to classify medium and high fire load in BS 5306 and this leaves a loop hole for the entire interpretation of the design engineers which we believe should be fixed in near future when revising the BS standards.
Next would be decision on what type of sprinkler points to be installed. For ordinary hazard, a 15mm orifice size of any type can be installed.
For high hazard CEILING OR ROOF SPRINKLERS, care must be taken in selection of sprinkler points. Only conventional or spray types with minimum 15mm orifice size can be used.
For intermediate sprinklers in piled storage, only conventional type sprinklers of 15mm and above size are allowed.
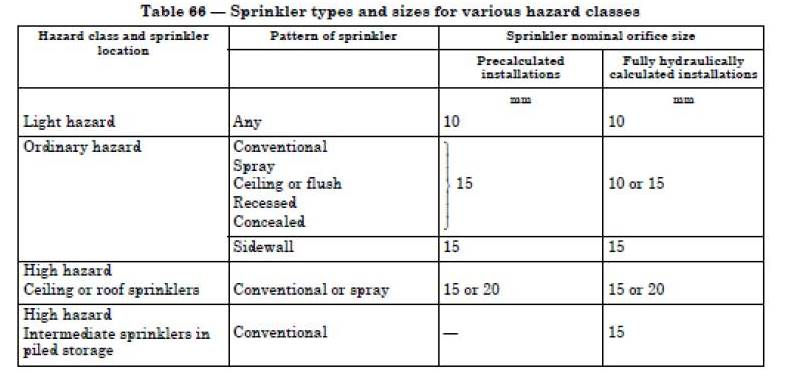
Having decided on all the above aspects only can the design for sprinkler system commence whether precalculated or fully hydraulic calculated in accordance to BS5306 or MS1910.
The next task would be to decide on the number of stages of the sprinkler system, the location of the sprinkler tanks, alarm gongs, breeching inlets and pump room. Sprinkler tanks should ideally be positioned next to pump room which is required to be at ground floor and access to pump room should be directly from external or via protected corridor inside building. At no time should the fire officers be required to expose themselves to fire risks when accessing the pump room.
When installing sprinkler tank at lower level than pump, care must be taken to avoid cavitation of the pump. Pump selection should be limited to pumps with low NSPH and foot valve must be installed at pump suction. Foot valve installation should be direct to pump inlet and should never be common. If required expansion tank should be installed before pump inlet as per BS5306 installation.
Alarm gong should be installed where the sound of alarm is audible to external of building. It should preferably be on ground floor except where sprinkler stages exceed the pressure rating for alarm gongs if positioned on ground floor. Then alarm gong and the higher stage pumps can be installed at higher level plant room.
Written by:
Ir. Tan Yoke Lee
IFE UK registered
コメント